The repair mortar developed for the construction of concrete structure track slabs and bridge slabs of high-speed railway elevated bridges is made of high-quality Portland cement, well graded silica sand, and composite imported high molecular weight polymers. It is a single component polymer special repair mortar with high early strength, excellent flexibility, and bonding strength. Widely used for repairing and reinforcing defects in concrete structure track slabs, bridge slabs, and bridge piers and abutments. Especially suitable for leveling construction of high-speed railway box girder bridge deck, meeting the durability requirements of high-speed railway engineering.
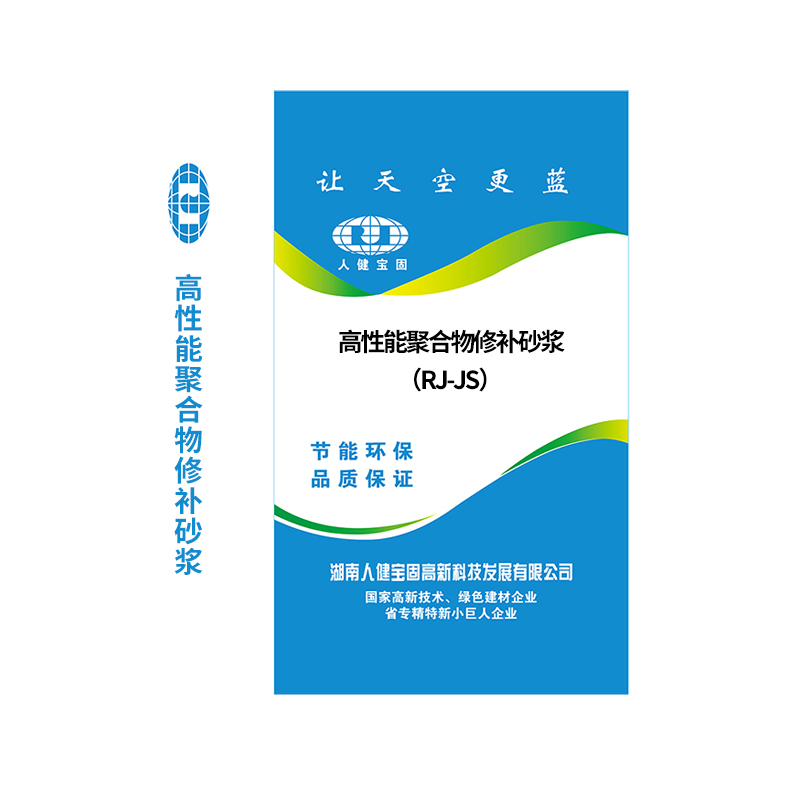
一、Product Introduction
The repair mortar developed for the construction of concrete structure track slabs and bridge slabs of high-speed railway elevated bridges is made of high-quality Portland cement, well graded silica sand, and composite imported high molecular weight polymers. It is a single component polymer special repair mortar with high early strength, excellent flexibility, and bonding strength. Widely used for repairing and reinforcing defects in concrete structure track slabs, bridge slabs, and bridge piers and abutments. Especially suitable for leveling construction of high-speed railway box girder bridge deck, meeting the durability requirements of high-speed railway engineering.
二、Main characteristics
Targeted construction can be carried out according to different parts;
The construction process is simple, just mix with water;
High early and late strength: 24-hour compressive strength greater than 30MPa, 28 day compressive strength greater than 60MPa, meeting the needs of rapid rescue and strength requirements;
Good adhesion performance: The coating has strong adhesion without the need for interface agents, and has excellent adhesion performance when bonding with concrete and mortar. It is resistant to frost and sulfate corrosion, non-toxic, non corrosive, and has good environmental protection;
Good crack resistance: able to adapt to the deformation of concrete base without cracking or falling off. There is no cracking, peeling or peeling phenomenon during thin layer repair;
◎ Has good anti sagging performance, suitable for vertical and top operations;
Can be used in damp substrates and environments, and can be used as repair materials.
三、Technical Parameter
Basic performance item |
Specification requirement |
TENGDA's personality indicators |
||
Slurry property |
Splitting tensile strength |
≥7 |
9 |
|
|
Flexural strength |
≥12 |
12 |
|
|
Compressive strength /MPa |
7d |
≥40 |
40.0 |
|
|
28d |
≥55 |
60 |
Bonding power |
Shear strength bonded to wire rope |
Standard value |
≥9 |
9.5 |
|
|
Mean value |
≥11.5 |
12 |
|
Positive tensile bond strength with concrete |
≥2.5, and it is concrete Cohesive failure |
≥2.5, and it is concrete Cohesive failure |
四、Application scope
High speed railway box girder bridge deck flatness repair;
Repair and reinforcement of defects in concrete structures (beams, bridge piers or abutments);
Repair of surface cracking hanging blocks on concrete beams, load-bearing columns, bridge decks, and outdoor thin plates;
Strengthening the repair of surface defects such as beams, columns, basement walls, etc. in large buildings and real estate projects;
Restoration and reinforcement of ancient and old buildings.
五、Usage
Before construction, the areas that need to be repaired should be marked, and the concrete base surface in the area should be solid, clean, free of oil stains, floating dust, loose objects, and other stains;
Use mechanical or manual methods to chisel and groove the concrete base surface in the construction area, then rinse it clean with water and fully wet it. When repairing and plastering, it should be ensured that there is no visible water on the surface of the concrete base layer;
Mix polymer repair mortar according to the recommended water cement ratio of 0.14-0.16. When using mechanical mixing, the general mixing time is 2-3 minutes. For manual mixing, the mixing time should be appropriately extended until the slurry is uniform and free of lumps, and then it can be used;
Use a spatula to scrape the mixed repair material onto the surface to be repaired, and promptly carry out calendering treatment. The thickness of each batch should not exceed 5mm. If it is too thick, it should be scraped in layers. After the surface solidifies and dries, it should be moisturized and cured. The plastic film lining the packaging bag can be covered on the surface of the repair mortar;
The mortar constructed in summer should be protected from direct sunlight, and the plastic film lining the packaging bag can be covered on the surface;
During winter, attention should be paid to insulation and maintenance. Hot water mixing and covering with rock wool blankets can be used for insulation. Construction cannot be carried out on rainy days or when the temperature is below 5 ℃ and the wind speed is above level 5.
六、Storage conditions and applications
Storage: Store in a dry and cool place, with a moisture-proof isolation layer at the bottom and a plastic cloth covering the top to prevent rain, water, and moisture. Ensure ventilation and avoid direct sunlight;
Under normal storage conditions, the storage period is 90 days. If it exceeds 90 days, it must be verified through testing before use;
Packaging: Paper bag packaging, 25kg/bag, 50kg/bag.
This product refers to the "Technical Specification for Safety Appraisal of Engineering Structural Reinforcement Materials" GB50728-2012 standard