The high-strength non shrinkage grouting material independently developed and produced by the Human Health Technology Center is a repair and reinforcement material composed of cement-based modified with various functional additives. It is divided into various types such as ordinary type, reinforced type, high-strength type, freshwater underwater type, seawater underwater type, etc. It has the characteristics of good adhesion to the base layer, oil resistance, good fluidity, no shrinkage, high early strength, and high durability. The slow increase in strength of the finished product in the later stage can effectively prolong the service life of concrete structures. The production and use processes are non-toxic and pollution-free, and belong to green and environmentally friendly products. They can be widely used in buildings, high-speed railways, roads, bridges, tunnels, seaports, equipment bases, bridge pier bases, dock foundations, repair and reinforcement of high-rise building pile foundations, underwater grouting, etc.
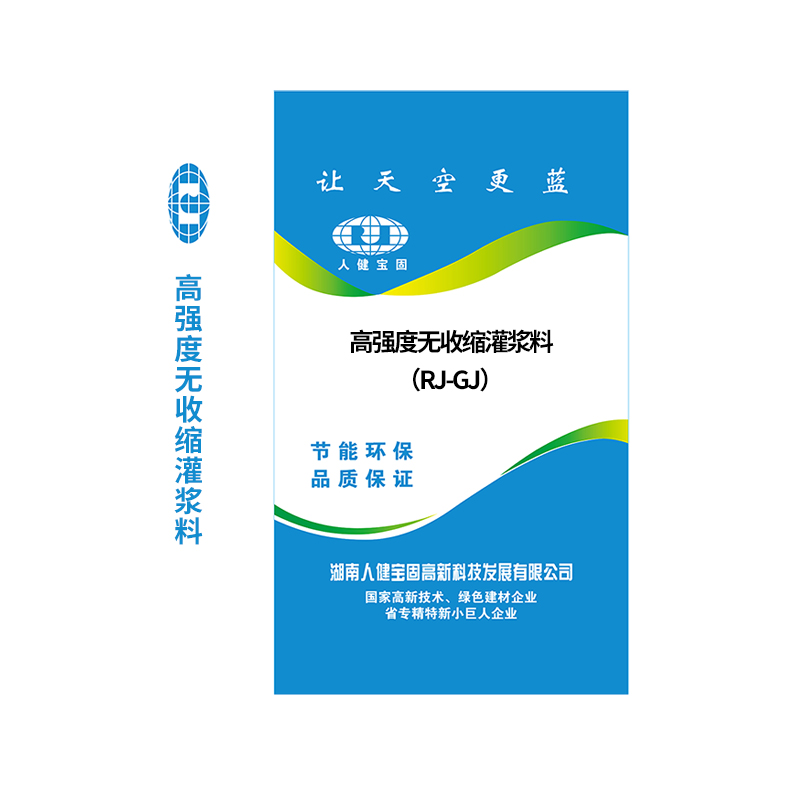
一、Product Introduction
The high-strength non shrinkage grouting material independently developed and produced by the Human Health Technology Center is a repair and reinforcement material composed of cement-based modified with various functional additives. It is divided into various types such as ordinary type, reinforced type, high-strength type, freshwater underwater type, seawater underwater type, etc. It has the characteristics of good adhesion to the base layer, oil resistance, good fluidity, no shrinkage, high early strength, and high durability. The slow increase in strength of the finished product in the later stage can effectively prolong the service life of concrete structures. The production and use processes are non-toxic and pollution-free, and belong to green and environmentally friendly products. They can be widely used in buildings, high-speed railways, roads, bridges, tunnels, seaports, equipment bases, bridge pier bases, dock foundations, repair and reinforcement of high-rise building pile foundations, underwater grouting, etc.
二、Main characteristics and technical parameters
Good fluidity, even in low water cement ratios, can still achieve a large fluidity and completely fill the space;
Convenient construction, ready to use with water mixing, and can also be filled with equipment to accelerate construction speed and save labor costs;
Micro expansion, no contraction, ensuring seamless filling space;
High early strength, with a 1-day compressive strength of 25MPa;
High durability, made of inorganic materials, does not age, does not corrode steel components, and is durable and sturdy;
Long service life, wide adaptability, non-toxic and harmless, environmentally friendly product.
item |
Technical parameter |
|||||||
|
Type I |
Type II |
Type III |
Type IV |
Fresh water type |
Seawater type |
||
Truncated cone fluidity |
Initial value(mm) |
|
≧340 |
≧290 |
≧650 |
|
|
|
|
30mim(mm) |
|
≧310 |
≧260 |
≧550 |
|
|
|
Cone fluidity |
Initial value(mm) |
≤35s |
|
|
|
|
|
|
|
30mim(mm) |
≤45s |
|
|
|
|
|
|
Compressive strength(MPa) |
1d |
≧15 |
≧20 |
≧25 |
≧35 |
≧8 |
≧8 |
|
|
3d |
≧30 |
≧40 |
≧45 |
≧60 |
≧12 |
≧12 |
|
|
28d |
≧50 |
≧60 |
≧70 |
≧85 |
≧30 |
≧30 |
|
Bleeding rate |
≧14 |
≧16 |
≧8 |
≧8 |
||||
Corrosion of steel bars |
No corrosion on steel bars |
|||||||
Vertical expansion rate |
3H |
0.1%~3.5% |
||||||
|
The difference between 24H and 3H expansion rate |
0.02%~0.5% |
||||||
For cement-based grouting materials with compressive strength grade A85, the 3H solid expansion rate index can be relaxed to 0.02%~0.35% |
三、Application scope
Used for reinforcing various types of concrete, embedding construction joints, and secondary pouring of steel structures;
Pouring of equipment installation base;
Repair and reinforcement of highways, bridges, tunnels, bridge piers, basements, and building beam and column foundations;
Repair and reinforcement of port terminals, bridge pier foundations, dock footings, high-rise building pile foundations, underwater grouting, etc.
四、Usage
Surface treatment: The construction base surface shall not have crushed stones, floating slurry, dust, oil stains, release agents, etc. Before grouting, the base surface should be fully moistened, but there should be no visible water;
Determine grouting method: Select the corresponding grouting method based on the construction site conditions. In general, the "self weight method grouting" can be used, which means that the grout is directly injected from the template mouth, completely relying on the self weight of the grout to level and fill the entire grouting space; If the grouting area is large, the structure is complex, or the space is small and the distance is far, "high-level funnel grouting" or "pressure grouting" can be used to ensure that the grout can fully fill every corner;
Mixing: Add clean water in a mixing container at a ratio of 100:14, then slowly add the dry mixture. Use mechanical force to stir until the powder is completely wetted and dispersed, and the slurry is dense and uniform. Do not dilute too much. Do not prepare too much slurry at once, it is advisable to use it up within 45 minutes;
Construction: During the construction process, taking advantage of the good fluidity of the grout, the grout is allowed to flow freely within the grouting range. It is poured from one side until it overflows from the other side, which is beneficial for releasing air and making the grouting material full. After the infusion begins, it must be carried out continuously without interruption. After grouting is completed, the surface of the finished product should be sealed before final setting.
五、Precautions and Applications
Maintenance: After the final setting of the grouting, it should be immediately covered with moisture for maintenance, but excessive watering should be avoided to prevent surface dust from appearing;
After the initial setting of the mixed material, it cannot be reused;
After construction, the equipment should be promptly cleaned with water for future use;
For special engineering requirements such as strength, negative temperature, setting time, or bonding strength, please contact our technical personnel;
During transportation and storage, it is necessary to prevent bag breakage and moisture prevention;
Under normal storage conditions, the storage period is 90 days. If it exceeds 90 days, it must be verified through testing before use.